Measuring & Testing Technology
for Production
MagHyst® is the ideal solution for the quality control of the electromagnetic actuator manufacturing.
Compared to conventional test methods, which are limited to the end-of-line test, MagHyst® automation offers the possibility to analyze the entire manufacturing process along the entire value chain and thus creates the conditions for the implementation of the zero-fault strategy.
Increasingly important is the control of the magnetic properties of raw materials and ferromagnetic purchased parts. Changes in the supplier's process as well as batch variations have a direct impact on the quality and performance of the finished actuators. With a MagHyst®-based incoming goods inspection, the incom of defective components can be avoided right from the start of the manufacturing process.
Within the in-line test, the influence of individual processing steps as well as the quality of the assembly can be controlled. Due to the extremely short measuring and evaluation times, MagHyst® automation is particularly suitable for monitoring adjustment processes for determining the armature position and adjusting the air gap.
MagHyst® automation is also used in the final goods inspection or as a Q-Gate before a fluidic tests.
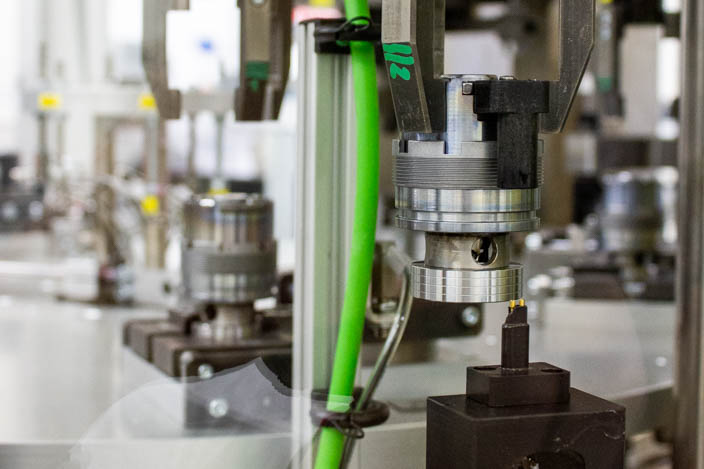
The following manufacturing failures can be detected and the respective cause of the error specifically identified:
- Friction in the overall system
- Residual air gap
- Spring preload
- Short circuits between the windings
- Contact errors
- Missing parts
MagHyst® automation can be used as a fully and partially automated test station for 100% testing as well as for sampling inspection. The system is characterized by an automatic evaluation of the measurement data, interfaces to the the PLC and comprehensive archiving of all measurement and evaluation data.